PUNCHING
打ち抜き加工技術
打ち抜き加工技術とは、両面テープ・フィルム・クッション・金属箔などの比較的低硬度の材料を、必要に応じて貼り合わせを行い、ビク(トムソン)型・ピナクル型・プレス型に代表される金型を材料に押し付ける事で、必要とされる形状を作り出す加工技術です。ビク型・ピナクル型の加工は、お菓子作りで用いられるクッキー生地を、型を利用して抜き取る様をイメージしていただくとわかりやすいです。
この加工技術は、高い量産性と精度に加え、汎用性も極めて高いため、様々な製品製造で用いられています。
当社は、時代に合わせて変わっていく、「新たな材料、新たな構成、より高い精度」といったお客様のニーズを、打ち抜き加工技術を磨くことで実現してまいりました。今後も、ますます高まるニーズに応えるため、未来の打ち抜き加工技術の確立を目標に、日々試行錯誤を繰り返しています。
打ち抜き加工技術の種類
打ち抜き加工の工程例
打ち抜き工程 概要図
当社の打ち抜き加工の概要図になります。
当社で設計した指示書をもとに、事前に必要な材料を必要な幅にカット、貼り合わせ等を行い打ち抜き加工機に投入します。
その後、投入された材料は、必要に応じて複数回打ち抜き加工され、不要な部分の除去、機能性材料の貼り込み等を行い、
最終的にシートカットを行うことで、製品として完成します。
このように一連の作業を連続的に処理できるよう、設備を効率的に配置しております。
当社ではこの生産設備を総称して「ワンライン」と呼んでおります。
この仕組みにより、生産効率が高まりコストを抑えた大量生産が可能になっております。
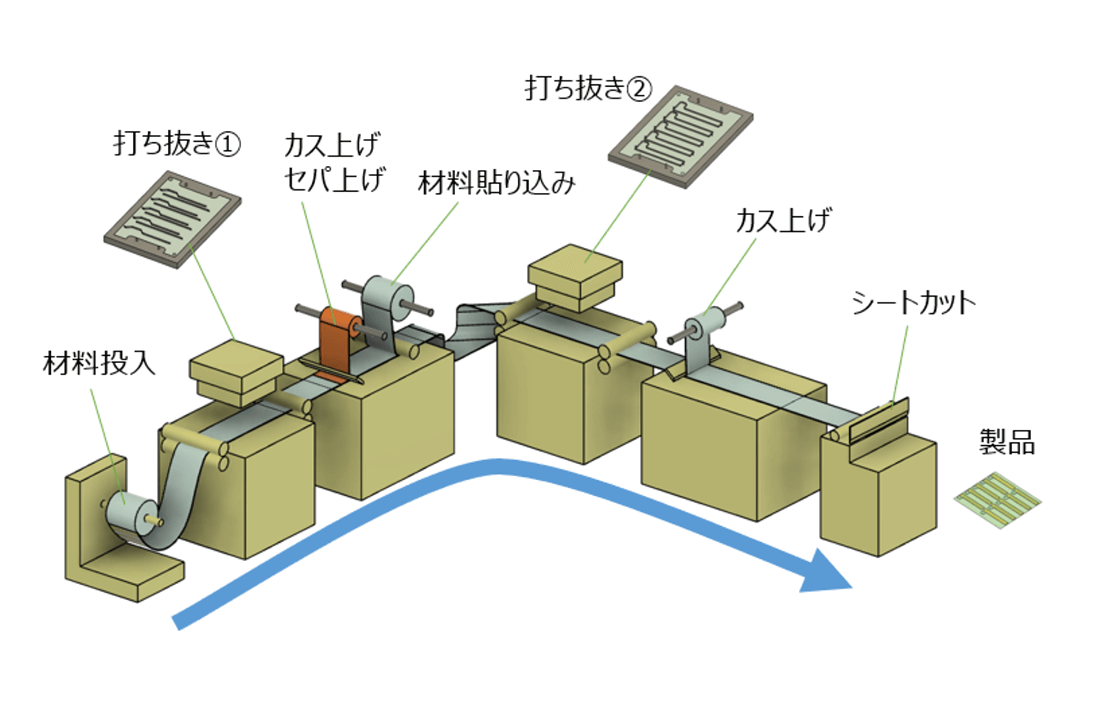
打ち抜き・・・主に型を使用して加工すること。
カス上げ・・・不要部を除去すること。
セパ上げ・・・セパレーター上げの略称で、不要なセパレーターを除去すること。
材料貼り込み・・・セパ上げ後、テープの糊がむき出しになるため、その製品に適した機能性材料を貼り込むこと。
シートカット・・・製品が貼りついているシートを任意のサイズにカットすること。
各工程毎の加工状態
以下の図は、材料投入されてから最終的な形状に仕上がるまでの間で、材料がどういった変化を辿るのかを分かりやすく視覚化したものとなります。
異なる様々な材料形状が複合するような製品の加工を行う場合、一般的に複数の段階に分けられた種々の打ち抜き加工が順を追って行われますが、当社ではこれまでの培ってきた経験や技術を活かし、完成までに必要となるそれら一連の作業を「ワンライン」化させています。
また、そういった工夫により生産効率が高まり、コストも抑えた大量生産を実現させております。
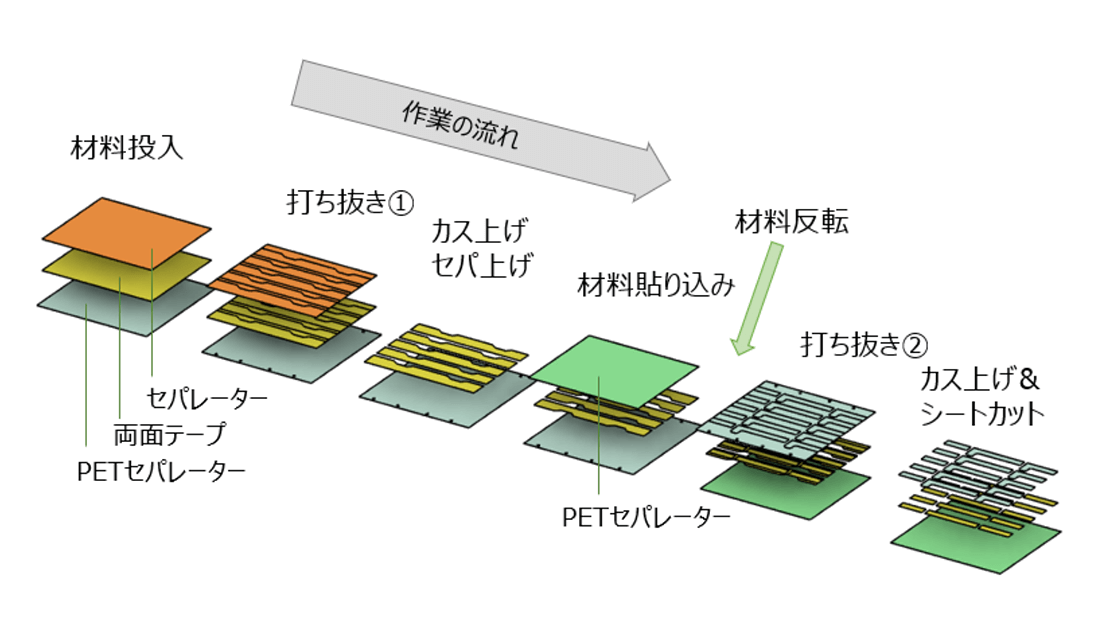
打ち抜き加工の金型説明
型の特長
型名 | ビク型 | ピナクル型 |
---|---|---|
作成方法 | 刃を加工後カットして ダイボード(ベニア板)に装着 | エッチング加工後に 刃をシャープニング加工(研磨) |
作成費用 | ◎ | △ |
作成期間 | ○ | △ |
加工精度 | △(つなぎ目有) | ◎(つなぎ目無) |
寿命 | ○ | △ |
金型が不要な打ち抜き加工
当社では、金型を使用しない打ち抜き加工を行うための裁断機を保有しております。
この裁断機(スーパーカッター)には1本の刃が装着されており、材料を設定された寸法の矩形形状に連続加工することができます。
加工方法としては、機械に材料をセットし、材料の横軸方向用のパラメータを用いて材料を1度目の自動断裁にかけます。
続いて材料を90度回転させた後、縦軸方向用にパラメータの変更を行い再び断裁にかけることで、連続する矩形形状へと材料を加工していきます。
このように金型を使用する加工方法と異なり、矩形形状に仕上がるまでに複数の段階を踏む必要がありますが、寸法変更の度に金型製作の費用が発生せず、さらには矩形の寸法指定もパラメータの変更だけで完結させられるため、開発段階の試作品や少量生産品の加工の場面で重宝されます。
また金型が不要になるため、短納期での納入も可能になります。
スーパーカッター・・・1本刃による矩形製品の連続加工用
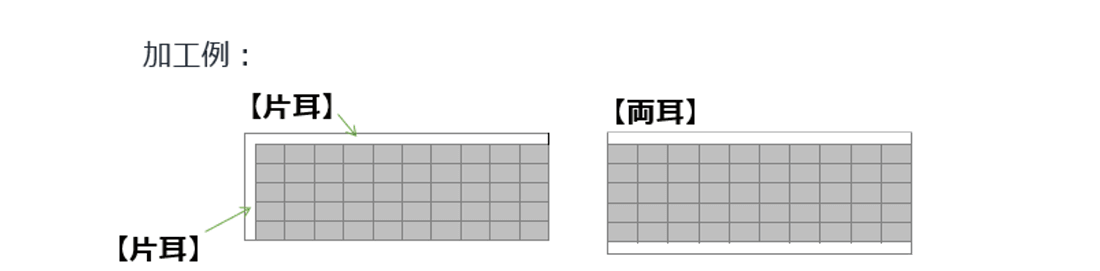
一列カス取した部分を「耳」と呼んでいます。
こちらは、当社のノウハウに基づいた取り組みでございます。
先ほどご説明申し上げました断裁機は、互いに直交する材料の2つの軸に沿って材料を動かしながら断裁を行います。
しかしこのような連続加工には、材料に刃が入る度に累積していくミクロンオーダーの位置ずれの問題が付随します。
特に、両面テープやテープ付きの材料の加工においては、それがセパレーター(台紙)部からの糊のはみ出しという別の問題を引き起こし、製品の品質や見た目に影響を与えることになってしまいます。
この問題を解消するため、当社では「耳」と呼ばれる部分を一箇所作成し、材料の位置ずれをセパレーター内部で抑える工夫を施しております。
また「耳」を設けたことは、セパレーターから簡単に製品を剥がすことを可能にし、お客様が手に取る製品の品質の向上だけでなく、使いやすさの向上にも寄与しています。
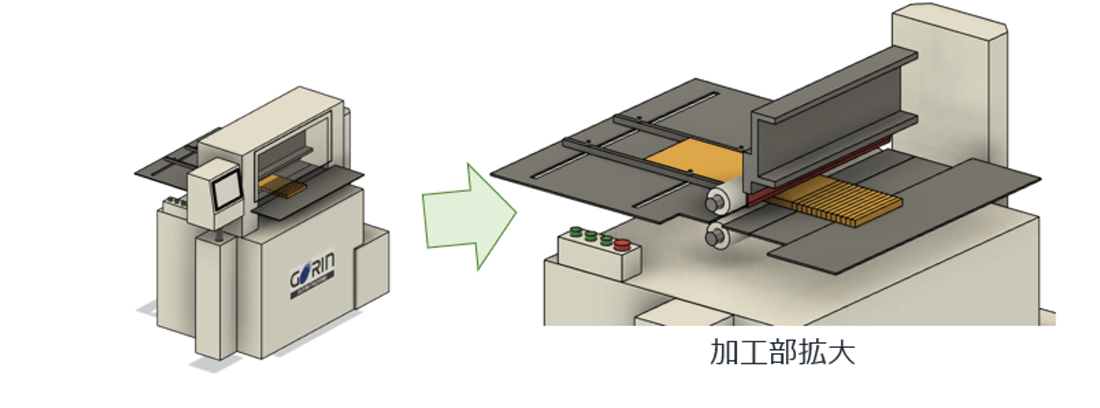
総抜き(フルカット)、半抜き(ハーフカット)について
当社では、上記でご説明した加工方法として「総抜き加工(フルカット)」および「半抜き加工(ハーフカット)」の両方に対応しております。
以下に、それぞれの加工方法について詳しくご説明いたします。
総抜き加工(フルカット)
総抜き加工とは、材料を貫通させて打ち抜く加工方法です。
こちらの加工方法では、シート納入では取り扱いが難しい製品や、最初から穴を除去しておく必要がある製品など、お客様のニーズに合わせた形状をご提供することが可能です。
半抜き加工(ハーフカット)
半抜き加工とは、材料を貫通させずにセパレーター(台紙)を残したまま加工する方法で、総抜き加工と比較して作業者に技術力が求められる加工方法になります。
こちらの加工方法は、複数の製品が同一シート上に配置されることになるため員数管理がしやすく、さらにコスト面でも優れているメリットがあります。
また以上の理由から、この半抜き加工は当社が標準採用する加工方法の一つとなっております。
COLUMNS
技術コラム
- 2025/4/18(金)
- 当社の生産
- 2025/3/26(水)
- 「ビク型」と「トムソン型」の違いについて