COLUMNS
技術コラム
2024/12/23(月)
厚手の発泡体(クッション)の打ち抜き加工
当社では、両面テープ、フィルム、クッション、金属箔など、多様な機能性材料の打ち抜き加工を行っております。
これらの材料はそれぞれ独自の特性を持っていますが、加工のしやすさに差があり、必ずしも容易に加工できるものばかりではありません。
また、材料それ自体が持つ優れた特性を最大限に活かすためにも専門的なノウハウや加工技術が必要であり、当社ではこうした課題に向き合いながら、各種材料に応じた最適な打ち抜き加工を追求しています。
今回は 厚手の発泡体 (クッション) の打ち抜き加工 について、事例を交えながら当社の取り組みをご紹介いたします。
従来の厚手発泡体の打ち抜き加工の課題
従来の発泡体の打ち抜き加工では、製品形状に合わせた型を使用して加工を行っていました。
しかしながら、厚みが刃の高さを上回る厚手発泡体については材料を潰しながら打ち抜く必要があり、以下のような課題がありました。
- 断面の「オチョコ状態」
加工後の断面が「オチョコ状態」(中心のくびれた形状)となるため、見栄えや機能性に影響を与える場合がありました。 - 加工精度の不安定さ
寸法精度が保証できず、高い精度を求められる製品には適用が難しいことがありました。 - コストの増加
精度を確保するためにウォータージェットなど他の加工方法を採用するケースもあり、コスト増につながることがありました。
上述の通り、打ち抜き刃の高さを上回る厚みを持つ「厚手発泡体」の打ち抜き加工では、打ち抜き刃が貫通する高さにまで材料を潰す過程が生じます。
さてここで、上図のように材料が潰された状態でそのまま打ち抜きが行われた場合、どういった問題が起きてしまうでしょうか。
物体の大変形に関する厳密な議論は非常に複雑になりますが、その問題の大まかなイメージ程度であれば、以下の単純化された材料変形のアニメーションから掴むことができるでしょう。
つまり、変形した状態で真っ直ぐ打ち抜きが行われてしまうと、力の作用が解かれて元の変形前の状態に戻った際、切断面上の各点に生じてくる一様でない水平方向の変位によって切断面がくびれてしまうのです。
そしてくびれてしまった切断面の様子をオチョコにたとえて、ここではその状態のことを「オチョコ状態」と呼んでいます。
現在の厚手発泡体の打ち抜き加工技術
当社では、従来の課題を克服するため加工技術の改善に取り組んできました。
特に、断面の「オチョコ状態」を抑え寸法精度を向上させるために、以下の改良を行いました。
- 型設計の工夫
発泡体にかかる圧力を適切に分散できるよう型設計の方法を見直しました。この工夫により、加工時の断面の歪みを大幅に軽減することが可能となりました。具体的な設計内容についての詳細をお伝えすることはできませんが、当社のノウハウによって精度の高い加工を実現しています。 - 材料特性に基づく型設定値の最適化
材料ごとの特性に応じた最適な型の設定値を採用し、加工精度を向上させています。この取り組みによって、従来よりも高い寸法精度を実現することが可能となりました。
またこれらの結果として、さらに次のような改善効果も得られています。
- 生産スピードの向上
多面での加工による、生産スピードの向上を達成しました。 - コスト削減
ウォータージェット加工などの他の加工方法に比べて、より低コストでの加工が可能となりました。
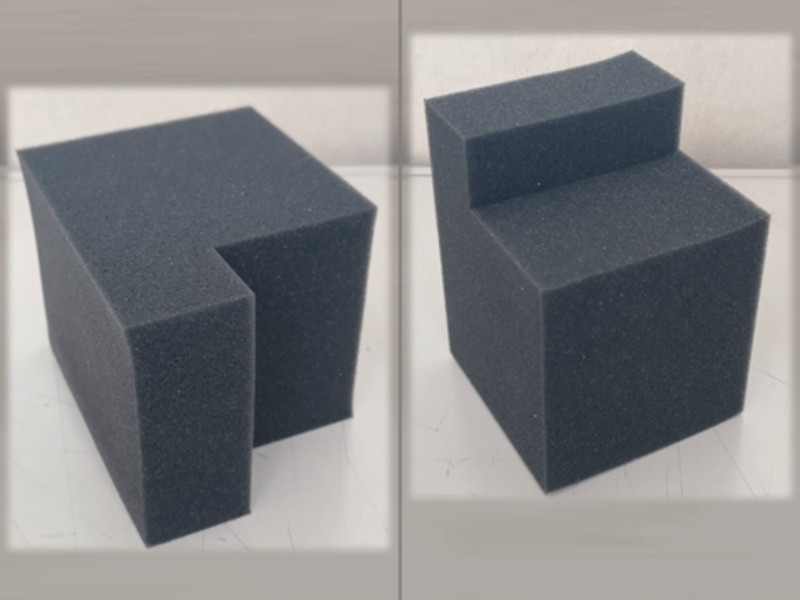
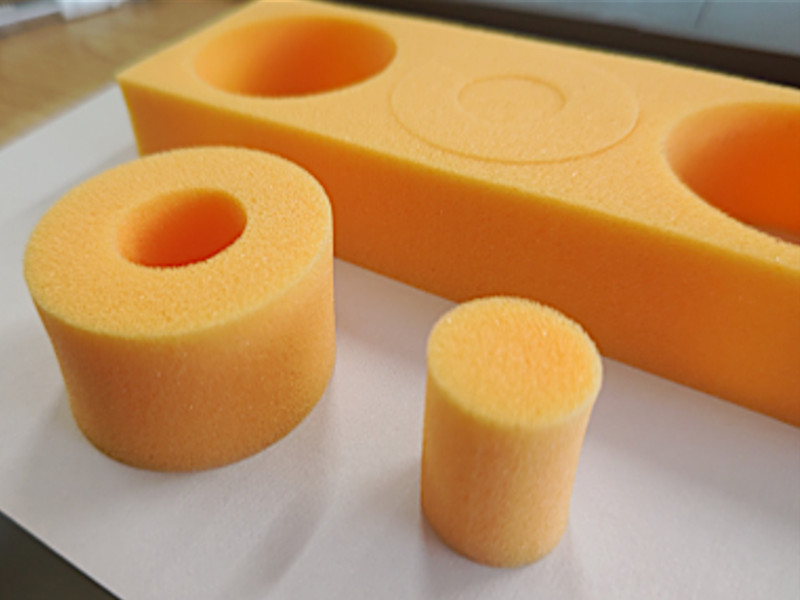
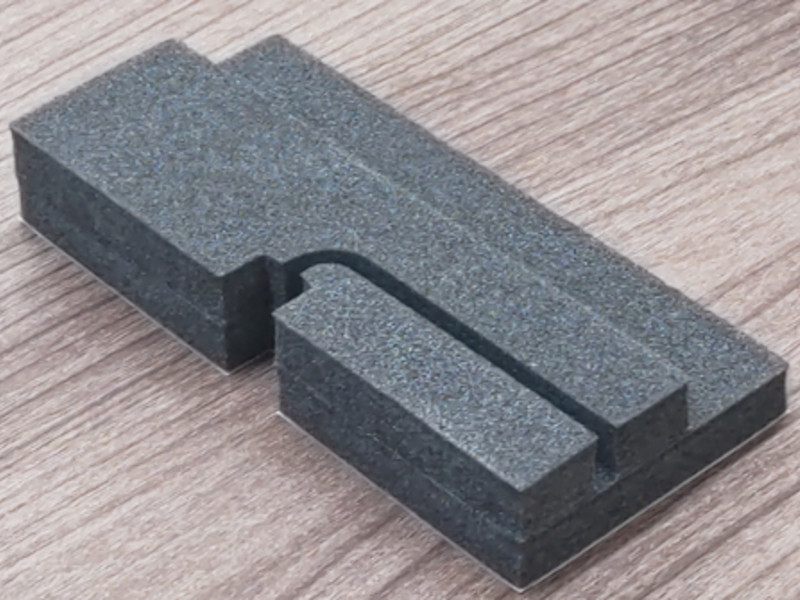
このように当社では、日々技術の改善や工夫を重ねることで、より良い製品をより安価でお客様にご提供できるよう努力しております。
材料特性に応じた最適な加工方法や精度の高い仕上がりを追求し、お客様のご要望にお応えするための取り組みを継続しています。
加工に関するお悩みや課題、ご相談がございましたら、是非お気軽に当社までお問い合わせください。